日立の高効率モータのカギは応力対策
7月9日に日立製作所が発表した、効率96%と高い、アモルファス鉄心を使ったモータ(図1、2)は、材料の加工がカギだった。今回試作したモータは、国際高効率規格の最高レベルに相当するIE 5をクリアしている。これまでの最高クラスといえよう。
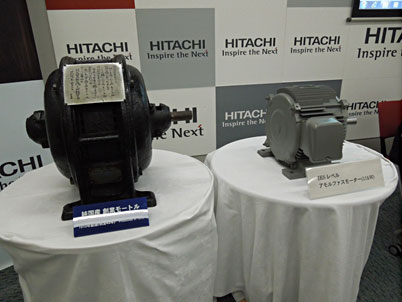
図1 日立製作所が開発した効率96%のモータ(右)
図2 効率96%でIE 5をクリアした11kWの高効率モータ
日立は2年前にIE 4という一つ低いレベルをクリアしたモータを発表している。この時の効率は、負荷トルク100%という条件で93%であった。それを96%に上げたことがどれほどすごいか。日本国内の産業部門の消費電力は全体で年間4,850億kWh。この内、モータが占める割合は約75%にあたる年間3,600億kWhと最も大きい。もし産業用モータの効率を1%上げるとその省エネ効果は36億kWh/年となり、この数字は原子力発電所1基分に相当するという。今回3%上げたモータを国内産業全体で使うと仮定すると、原発3基分の省エネになる。
アモルファスの鉄板は通常の鉄鋼板に比べて透磁率が1桁高く、鉄損は1/10と低い。このため効率は高くなるはず。しかし、泣き所は、薄いアモーファス鉄板をモータのステータの形状に合わせて切断加工すると、磁性特性(磁束密度)が劣化したことだ。例えば、磁束密度が1.6T (テスラ) で鉄損がわずか1W/kgしかない生の特性が劣化し、鉄板を加工すると1.4Tで、16W/kgという鉄損が生じていた。
日立のエンジニアは、厚さ0.5mmの鉄心にコイルを巻いたHコイルと呼ぶ磁気センサを試作、実機に取り付け、アモルファス鉄心の磁気特性を調べた。損失を生み出していた要因は、加工する時の応力だという。アモルファス鉄は急冷して作るため、規則正しく鉄原子が並んでいない材料である。応力が加わると磁性特性が大きく劣化していた。このため応力をできるだけ減らすように、アモルファス鉄板の大きさや加工の仕方の最適値や最適方法を求めた。実際のデータと2次元・3次元の熱シミュレーションを利用して、損失すなわち熱の発生状況を可視化した。これによってアモルファス鉄心の損失を減らすことができたという。アモルファス鉄板1枚の厚さは25µmで、それを2000枚重ねて鉄心とする(図3)。その鉄心の周りにコイルを巻きつけて電磁石を作る。そのコイルの巻きつけ方に関しても応力が入るため、最適な巻き方を見い出したとしている。
図3 日立はアモルファス鉄心の磁気特性、熱特性を実測し最適形状を求めた
モータはアキシャルギャップ構造を採用しており、ステータの電磁石を円盤状の2枚のロータで挟み込む方式。コイルを巻きつけた電磁石を回転軸の周りに沿って十数個設ける(図4)。アキシャルギャップ方式では、2枚の永久磁石円盤ロータが回転する。今回、アモルファス鉄心の損失を少なくし、電磁石の磁力を強化したため、ロータの永久磁石にレアメタルを入れなくても十分な効率が得られた。
図4 アキシャルギャップ方式のモータを日立が開発
この高効率モータは、ポンプやブロアー、空気圧縮機(コンプレッサ)など製造装置に使う産業機械用途から実用化し、技術がこなれてくると自動車や小型モータなど広い用途に展開していく、と実用化を担当している日立産機システムのCTOで研究開発センタ長の相馬憲一氏は期待している。