マキシム、アナログの高集積化で成長を加速
米アナログ・ミクストシグナル半導体大手のMaxim Integratedは、これまでのシステムソリューションプロバイダから一歩先んじて、高集積という段階に踏み出した。同社は、社名もこれまでのMaxim Integrated Products社から、Maxim Integratedに変更した。これは、製品を売るだけではないというメッセージであり、戦略の大きな変更になる。Apple ComputerがAppleに変えたことと同じだという。
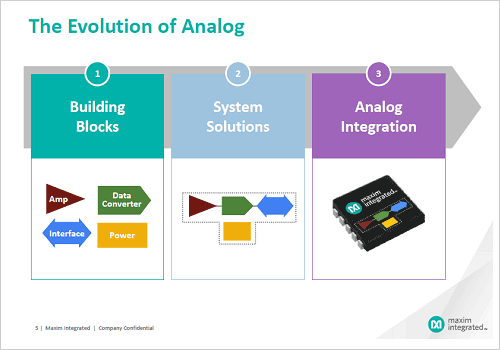
図1 アナログ差別化のカギは高集積化 出典:Maxim Integrated
今回の戦略を第3世代と名付けた。第1世代は、アンプやデータコンバータ、パワーマネジメントなど個別の製品を売っていた時代で、第2世代はそれら個別の製品をシステムに合わせたソリューションとして提供していた。今回の第3世代はアナログ高集積化、となる(図1)。
高集積化は顧客ごとの製品となりやすく、製造コストが高くなりがちだ。Maximがソリューションの延長として個別製品のまとめ売りではなく、集積化の1チップ売りに変えた背景にあるのは、同社の高集積製品の売り上げが急速に伸びてきているからだ。2007年には個別製品が82%に対して高集積製品は18%しかなかったが、2012年は37%にも及ぶと同社は見ている。
図2 アナログ高集積製品は2008年から2.5倍に成長 出典:Maxim Integrated
Maximの個別製品の売り上げは「2008年からほぼフラットだが、高集積化製品は、2.5倍に伸びた(図2)」と同社通信・自動車ソリューション担当上級バイスプレジデントのMatt Murphy氏は語る。逆に言えば、Maximは高集積化へシフトすることで売り上げを伸ばしてきたことになる。
図3 Maximの通信・自動車ソリューション担当バイスプレジデントMatt Murphy氏
スマートフォンに使われるアナログ製品で高集積化の動きを追ってみると、3年前のスマホ(図4のGen1)ではアナログ機能は42個、アナログとセンサの合計チップ面積は145mm2だったが、進化するにつれGen2ではアナログ機能が55個、合計面積188mm2、最近のGen3ではアナログ機能82個、合計面積192mm2となっている。ユーザーが求める機能が増えていることを反映しているとMurphy氏は言う。同氏は「この方向はスマホだけではない。カーエレクトロニクスや金融、エネルギー、医療、工業用などにも同様な傾向がある」と述べる。アナログの総面積の増加と対照的に、デジタル回路のチップ総面積は次第に小さくなっていく(図4)。
図4 アナログの機能は増える一方 出典:Maxim Integrated
集積回路一般に言えることだが、集積度を上げ、アプリケーションスペシフィックにすればするほど、数量は減るため製造コストは高くなる。これに対して、Murphy氏は3つの方法で解決していると言う。一つは前工程での200mmウェーハから300mmウェーハへの移行だ。高集積になればチップ面積は増加するため、200mmなら1枚のウェーハから採れるチップの数は少なくなってしまう。このため処理枚数を増やさなければならない。例えば、200mmだと50枚必要でも300mmでは21〜22枚程度で済む。現在、製品の20%は300mmウェーハを適用しているという。
製造上のコストダウンとして、多数使っていた後工程サブコントラクタを数社だけに絞り込んだ。1社当たりの処理量が増えることでコストを下げられる。3番目の方策として、製品の付加価値を顧客に訴求することである。顧客にとっては1チップ化することでボード面積が減りコストを削減できる。加えて、同社のアナログ高集積製品の民生比率を上げることで数量を増やし、コストダウンにつなげるとする。
ウェーハ製造にはMaximの持つ米国工場に加え、パートナーとの契約ファウンドリを活用する。同社はオレゴン州ビーバートン、テキサス州サンアントニオ、カリフォルニア州サンノゼにそれぞれプロセス工場を持っているが、2007年にフレキシブルファブを持つという決定をした。いわゆるファブライトであるが、外部ファウンドリの使い方をきっちり分けている。日本のセイコーエプソン酒田工場、台湾のPowerchip (300mm)と MaxChip (200mm)とパートナー契約を結び、Maximのプロセスレシピを提供し、アナログ製品を製造している。もちろん、レシピの外部流出を厳しく禁止する契約を結んでいる。一方、生産比率の低い一般的なデジタル製品はTSMCに依頼してTSMCのプロセスに合わせている。
高集積化によるもう一つ大きな変化は、外部との協力体制である。例えばスマホ用のパワーマネジメントチップの場合、ベースバンドやアプリケーションプロセッサのメーカーとも一緒にパートナーシップを組み共同で開発する。インテルやクアルコム、nVidia、ブロードコム、マーベルなどと一緒に開発しているという。1チップのパワーマネジメント半導体には22個の電源回路を集積しているものもあるため、パートナーとの協力は欠かせない。
Murphy氏は、Maximの日本法人、マキシム・ジャパンのトップを務めた経験があり、この9月に来日して日本の自動車メーカーを回った。日本のエレクトロニクスメーカーが現在、苦戦していることは理解しているが、同氏は決して悲観的にみていない。日本の顧客を回ってみてイノベーション能力のある企業がたくさんある上に、ハイレベルなシステムを考えているメーカーがいることもわかった。ICチップのデザインセンターは米国にあり、日本にはない。ただし、ファームウエアはマキシム・ジャパンが開発する。高集積なアナログチップにはプロセッサコアやステートマシンも集積されており、コントローラとしてのプログラム開発では、日本を重視している。