半導体プロセスはビッグデータ解析で生産性向上へ〜AEC/APC Sympo2013から
半導体製造におけるプロセスパラメータがあまりにも膨大になり、まるでビッグデータそのものの扱いと同様な分析法が求められるようになりつつある。さまざまな検索データや通信ログ、などの膨大なデータをクラウド上で処理するビッグデータの解析手法が、半導体プロセスのデータにそっくりそのまま当てはまるのである。
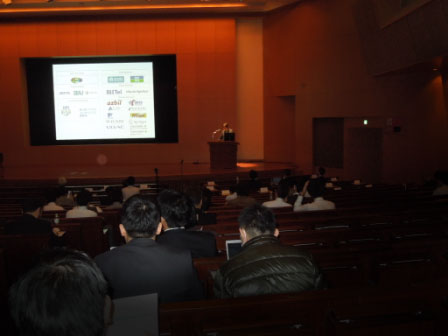
図1 AEC/APC Symposium Asia 2013の開会風景
半導体プロセスで使われるパラメータは極めて多い。温度や圧力、複数のガスの流量、プラズマパワーなど、さまざまなパラメータを大量のウェーハに適用していく。ウェーハは、FOUPカセットに入れられて処理されるが、カセット間、カセット内、ウェーハ間、ウェーハ面内、これらのバラつき要因を分析しようとすると、もはや膨大なデータ処理に匹敵する。
プラズマプロセスでは、チャンバの内壁に薄膜が堆積したり、内壁が削られたりするなど、厳密にいえばウェーハ1枚処理するたびに条件が変わってしまう。それもカセット同士の間でも変わる可能性がある。このため、チップの電気的特性とプロセス条件との対応が極めて複雑になっている。一つのパラメータを変えると、そのまま電気的特性に現れるとは限らない。半導体プロセスで使われている製造条件が、物理的にとらえきれなくなってきたのである。
2013年11月7日、東京で開催されたAEC/APC Symposium Asia 2013(図1)の基調講演に立った、東芝セミコンダクター&ストレージ社CIOの岡明男氏(図2)によると、工場のCIMシステムや製造装置、検査装置から毎日集まるデータは、1600Mデータにも及ぶという。ほぼ3年間の履歴データを積み上げると、ペタ(テラの1024倍、ギガの約百万倍)バイト級にもなるとしている。まさにビッグデータそのものである。
図2 東芝セミコンダクター&ストレージ社CIOの岡明男氏
AEC(Advanced Equipment Control)/APC(Advanced Process Control)は、半導体製造プロセスのバラつき変動や経時変化などをフィードフォワードなどによって制御する技術や装置の総称。この会議は、フィードバック/フィードフォワード制御と共に、モデルを立て統計的手法が欠かせなくなってきたことを示してきた。今年はさらに、ビッグデータの解析に必要なHadoop関数を半導体プロセスデータの解析にも使う方向が見えてきた。Hadoop関数は大きなデータをいくつかに分割し、複数のコンピュータで分散処理していく手法である。
半導体を歩留り良く、均一な高い品質で作るための総合技術は、ビッグデータを解析して、制御するようになる。岡氏によると、ビッグデータ解析時間はまだ遅いため、今後、装置データのオープン化や標準化などによって、処理時間の短縮を図る必要があると指摘している。