信越ポリマーが薄いウェーハ/支持テープ用樹脂製フレームを標準化提案
信越ポリマーは、3次元ICやSiP、薄型パッケージなどに欠かせない薄いウェーハを支持するリング状のフレームを従来のステンレスやアルミなどの金属からプラスチック樹脂に換え、その樹脂フレームを標準化する提案をSEMIに働きかけていたが、このほどSEMIで承認された。11月には300mmウェーハを対象とした樹脂フレームの標準化文書(英文)が発行され、2009年3月には日本語版も発行される見込みである。
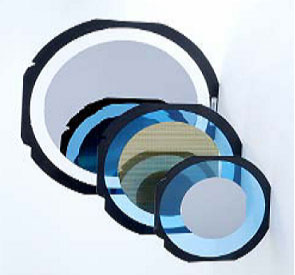
シリコンウェーハは、100μm以下に薄く削ると持ち運びにくくなるため、粘着性のテープに張り付けて取り扱うことが多いが、それを例えばウェーハ25枚入りのフレームカセットと呼ばれるキャリヤボックスに収めて運ぶには、外枠(フレーム)で固定する必要がある。このフレームを従来のステンレスから樹脂製に換えたものが信越ポリマーの開発した樹脂フレームだ。プラスチックテープに張り付けた薄いウェーハを支える樹脂フレームは、ダイシングプロセスとダイボンディングプロセスとの間、およびウェーハの出荷と搬送に使われる。
信越ポリマーが提案した300mmウェーハ用の樹脂フレームの厚さは2.5mm。ステンレスフレームの1.5mmと比べると厚いが、これは剛性を強くするため。ただし、これ以上厚くすると、標準的なダイボンダーのエキスパンドテーブルに載せるための3mmの隙間を通らなくなる。樹脂製フレームで先行した競合他社のフレームは3.7mmもの厚みがあり、従来の機械には載せられないため、専用の機械が必要とされた。樹脂フレームで強化したウェーハを利用する機械には、ダイボンダー、ウェーハマウンター、ダイサーなどがある。
金属フレームと比べて有利な点は二つ、軽量化と低発塵である。軽量化は、作業者が13枚のカセットを運ぶ場合の利点が大きい。300mmウェーハ用のフレームは従来のステンレス製だと1個0.3kgだが、樹脂フレームは0.12kgしかない。13枚のカセットに収容する場合ステンレスフレームだけで3.9kgにもなる。ここに13枚分のウェーハ(テープを張り付けたウェーハの重さは40g)とキャリヤボックス(ステンレス製5.9kg)が加わると、10.3kgにもなる。樹脂フレームは13枚分で1.56kgにしかならない。これにウェーハ13枚と容器(樹脂製キャリヤ3.0kg)を加えて5.1kgに収まる。作業者がカセットを持ち上げるのに10kgと5kgの差は大きい。
海外に後工程の工場がある場合は、ウェーハをテープフィルムに貼り付けその周囲をテープフレームで支持した形で出荷することが多い。それをキャリヤボックスに入れて梱包する。重量は輸送費のコストに影響する。
発塵が低いという利点も大きい。信越ポリマーによると、メタルのフレームを使ってカセットに出し入れしたメーカーがウェーハの電気的ショート不良が多発したことがあったという。原因はメタルカセットとメタルフレームとの摩擦によって金属の粉をウェーハ上にまき散らしてしまったためだとしている。この原因を特定するため従来のステンレスフレームと樹脂フレームとの比較実験を行った。
このフレームをカセットボックス(キャリヤ)に出し入れする時に発生するごみの量を調べた。300mmウェーハ用のテープフレームについて、ウェーハを張り付けた状態で、出し入れを1万回行った。1枚のウェーハの重さは128g。実験では、信越ポリマー製の樹脂製キャリヤボックスを用い、従来のステンレスフレームには従来のアルミ製のキャリヤボックスを使った。ステンレスフレームと樹脂フレーム、アルミのキャリヤと樹脂のキャリヤ、という4種類の組み合わせが可能になった。
この結果、ステンレスフレームとアルミのキャリヤボックスでは70mgの発塵を観測し、目視でもはっきりわかった。発塵の大きさは、10~300μmで、その成分はFe、Cr、Alとステンレスとアルミ成分が出てきたことから、摩擦により発塵が起きたといえる。樹脂製のフレームと樹脂製のキャリヤボックスは目視では観測されず、発塵の量は1mg以下であった。樹脂はポリカーボネート系であり金属を含まない。
一方、樹脂フレームとアルミのキャリヤという組み合わせでは、21mgの発塵が集まり、その成分はアルミと樹脂であった。発塵の大きさは2〜100μmと、ステンレス&アルミの組み合わせでの発塵よりはややましになった。金属の異物がウェーハに載ると、端子間がショートする危険性がある。