レゾナックが自らコンソーシアムを組織化する理由とは
旧昭和電工と旧日立化成工業が合併し、半導体に力を入れる化学材料メーカー、レゾナックは、これまでの合併劇とは全く異なる成長戦略を掲げている。それは仲間と手を組もうというエコシステム「Joint2」を構成している点だ。その中心にいてまとめ役としてレゾナックがある。同じような化学材料メーカーとのコラボは、技術情報が漏れるのではないかと心配する向きはある。それでもレゾナックは発展するだろう。なぜか。
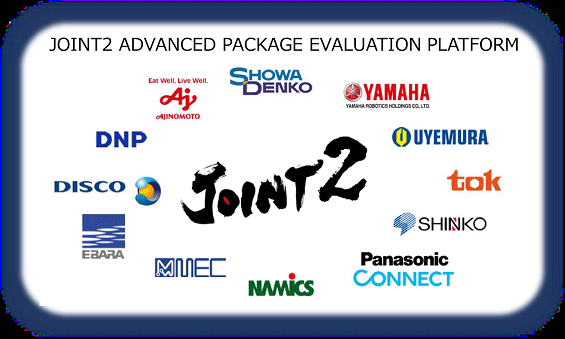
図1 レゾナックが仕掛ける先端パッケージ技術開発コンソーシアム「Joint2」 出典: レゾナック
共鳴(Resonance)とテクノロジーから社名を新たに変えた、レゾナックは半導体産業構造を詳細に分析した。Joint2プロジェクトは図1にあるように半導体材料や製造装置メーカーなどから構成されている。2021年にスタートしたJoint2プロジェクトは、2.5D/3Dの集積回路(IC)を作る先端パッケージングを開発する。
実は旧昭和電工・日立化成のグループは2019年からもコンソーシアムJoint1プロジェクトをスタートしていた。FOWLP(Fun-out Wafer Level Packaging)の開発が目的だったが、参加費なしで他の企業にも参加してもらった。しかし、2.5D/3D-ICの先端パッケージ技術だと、開発資金が急速に増える見通しのため、Joint2では国からの補助金と他企業からの参加費で賄われている。
図2 レゾナック開発センター長の阿部秀則氏
なぜ、このようなコンソーシアムが必要か。その理由を同社開発センター長の阿部秀則氏(図2)は語る。「半導体製造プロセスでは図3のようにさまざまな製造装置が担い、しかもつないでいく。例えば、露光装置を製造しているASMLは露光工程を受け持つが、その前後のレジスト塗布や現像、リンス洗浄などは東京エレクトロン、エッチング装置はTELやApplied Materialsなどの企業の装置へと受け継がれていく。後工程も同様な構成になっている」。だからこそ、前後の工程を受け持つ装置や材料の企業と協業しなければ、個々のプロセスを統合する場合の問題が明確にならない。プロセス統合する場合の問題点を早く見つけ、早く解決することが最大の目的となる。
図3 半導体前工程はさまざまな企業の装置を連携させて構成されている 出典:レゾナック
2.5D/3D-ICにおけるパッケージング技術では、Joint2プロジェクトの構成企業がうまく連携しながらトータルの後工程をつないでいく(図4)。例えば基板はレゾナックなどの企業が提供しても、多層配線のビルドアップ基板は味の素が得意。そのあとの配線工程や表面処理など別の企業が担当するという具合だ。このようにして各工程を連携していくと、共通の問題に出くわす場合には問題解決が早くなる。このすり合わせ作業がなければ、問題解決に時間とコストがかかってしまう。
図4 後工程や基板工程で様々な企業と連携しながら問題を共有すれば解決は早まる 出典:レゾナック
2.5D/3D-ICの開発は前工程に似てきた。微細なバンプ電極の形成では、シードメタル形成、レジスト塗布、露光、現像、洗浄などの工程を経て、メッキによる厚いメタルを形成し、レジストを剥離する。最後にシートメタルをエッチングしてバンプが完成する。こういった工程では1社の材料だけでは賄いきれない。レジストは東京応化、メッキは上村工業とそれぞれ使い分けていく。
レゾナックの開発センターは、様々な企業との連携が必要なため、つくばからもっとアクセスのよい新川崎地区に移転してきた。
レゾナックの観点からみると、昭和電工は素材の上流工程にある純粋な素材を、日立化成はさまざまな素材を組み合わせて、半導体メーカーの要求にあった材料(コンパウンド材料)を、それぞれ得意としていた。両社が一つの企業になることで、素材と材料をつなぎ、実際に使える材料を半導体製造企業に提供できる。ただし、これだけではプロセス全体をカバーすることができない。つまり、さらなる成長を狙ったエコシステムの構築といえそうだ。